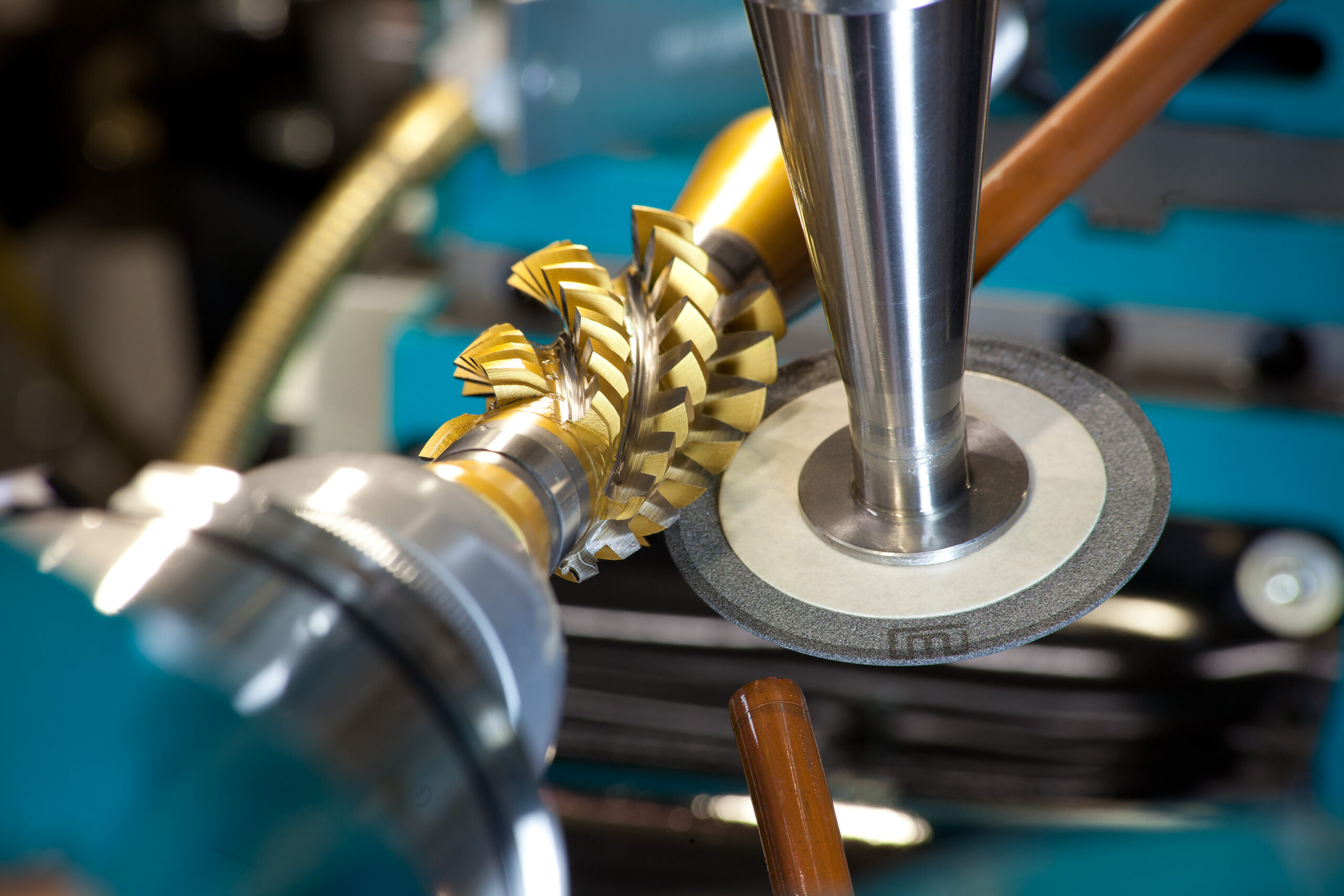
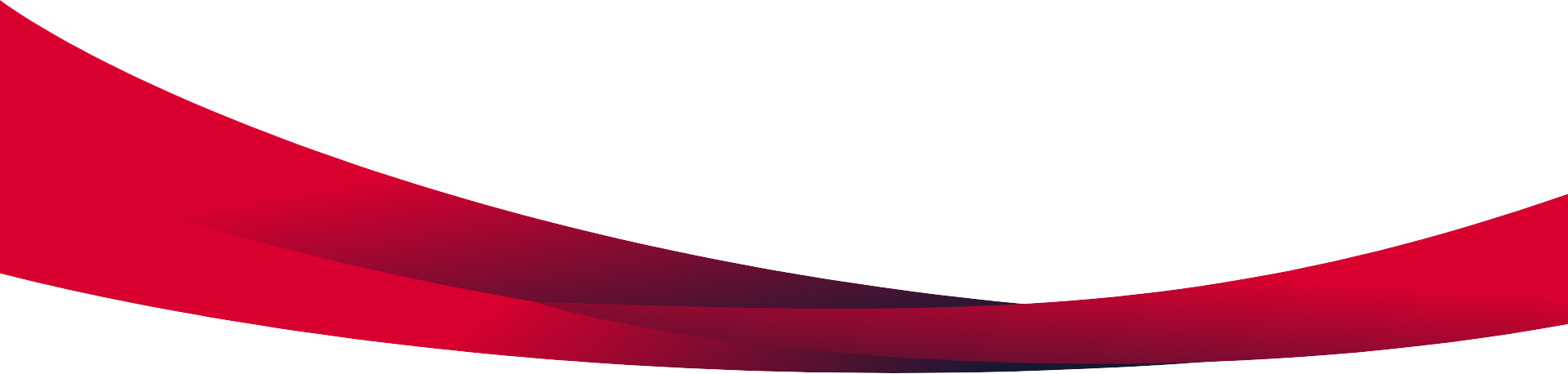
StingR® – Field report from Gesau-Werkzeuge Fabrikations- und Service GmbH
Filtering HSS without compromise
With the StingR ultra-fine filter technology, Lehmann-UMT has developed a hydropneumatic backwashing process that offers the user a number of advantages. For the tool company Gesau-Werkzeuge, one thing is paramount: mastering a particularly difficult filtration process when grinding gear-cutting tools.
Cooling lubricants are a crucial component in the machining process; often, a machining task would not be possible without them. Thus, the cooling lubricant preparation is also an indispensable component in the process, since the cooling lubricant supply must be maintained in the required purity and at the necessary flow rate. In turn, the degree of purity of the cooling lubricant has a significant influence not only on process stability but also on the machining result and the wear of the cooling lubricant constituents. However, the right technology can only be selected and configured with a precise analysis of the machining process and its requirements. Gesau-Werkzeuge Fabrikations- und Service GmbH has consistently followed this path. The tool specialist from Glauchau-Gesau has completed the final stage of a metamorphosis in the cooling lubricant preparation that has been driven forward for years with Lehmann-UMT.
Producing and processing special tools
The fact that this path was unavoidable can be seen directly from the range of services offered by the tool specialist. Founded in 1980 as a workshop for the regrinding of cutting tools, the company concentrated on tools for metalworking from the 1990s onwards and, in this context, developed from a craft business into an industrial service provider. Today, Kerstin Milenkov, daughter of the company founder, and Ulf Köhler are the owner-managers of the 35-strong company. The production in Glauchau-Gesau concentrates on rotating, monolithic shank tools, preferably made of carbide and HSS, but also Cermet or CBN. Milling and drilling tools are thus just as much a part of the portfolio as semi-finished products and precision parts. „Among other things, we have specialized in elaborate tools with large aspect ratios,“ reports Ulf Köhler. However, Gesau-Werkzeuge also manufactures special products from CBN and Cermet. The second area of activity for the company is tool grinding as a service. „In this segment, we specialise in gear-cutting tools with a geometrically determined cutting edge and repair all tools that work on the tooth flank,“ says the managing director. Gear hobs, he states for example, are ground in all dimensions and constructive designs up to quality grade AAA. In addition to accuracy, another challenge in resharpening is the dimension of the tools. „In terms of broaching tools, our largest tools are 3 m long and weigh up to 500 kg.“
When regrinding gear-cutting tools with dressable wheels, a corundum/HSS mass is produced which is difficult to filter out of the cooling lubricant (image: Gesau-Werkzeuge)
Marcus Ludwig, Lehmann-UMT Sales; Ulf Köhler, Gesau Tools Managing Director; Frank Enderlein, Production Manager and (from left) in front of a Lehmann filter system (image: Lehmann-UMT)
The challenge of corundum chip abrasion
This is also where Lehmann-UMT‘s filter technology is used for the preparation of gear-cutting tools. Why? Because it is a particularly delicate process: Some of the HSS tools have to be ground with dressable wheels, which results in a high amount of abrasive wear. Together with this corundum, the abrasion of HSS – which unlike carbide is a long-chipping material – forms a tough mass that places high demands on the filter technology. „That is why we went looking for a supplier that could handle these abrasion or contamination types with their filter technology,“ says Ulf Köhler. Up to this point, cooling lubricant preparation at Gesau-Werkzeuge has already undergone several stages of metamorphosis. Years earlier, the company invested in a centrifuge machine. With this central machine, however, they were limited to one type of cooling lubricant and had only a limited technological field of application at their disposal. It was a reliable wprocess, but lacked flexibility. In 2015, the tool specialist therefore began to decentralise again. A second circuit with a gap filter system was put into operation, which now filtered the cooling lubricant from the carbide grinding. „We immediately made a big leap in this area: in terms of quality, throughput and process reliability,“ reports production manager Frank Enderlein.
However, the corundum HSS mass remained a problem. „Here, we have four CNC machines that use dressable grinding wheels. For dressing them, we next wanted another cell, a third circuit that could handle this abrasion,“ says Ulf Köhler. „Today, we are at the finishing line of our metamorphosis and are using three cooling lubricant circuits: the large machine with centrifuge technology that handles mixed operations, the cartridge gap filter system designed for carbide machining, and the StingR system from Lehmann-UMT for the critical corundum/HSS slurry.“
The reason for the third, adapted cooling lubricant circuit at Gesau-Werkzeuge: tough corundum/HSS abrasion, which is difficult to filter (image: Lehmann-UMT)
As a multi-stage filter system, the StingR ultra-fine filter technology uses a hydropneumatic backwashing process in particular (image: Lehmann-UMT)
Multi-stage filter technology
The ultra-fine filter system from Pöhl which Gesau-Werkzeuge is using today, can basically be equipped with a magnetic separator, compact filter, scraper discharge system, lamella separator and a 5-stage filtration system. This provides a high degree of flexibility, enabling applications in machine tools, engineering and environmental plant construction as well as in the chemical industry or water treatment.
At Gesau-Werkzeuge, the StingR works in the first step with a lifting station which collects the fluid from the four machines and raises it to the level of the filter system via a dirt pump. „The first filter stage provides for a magnetic separator that removes all magnetic substances, but even at this stage also binds some non-magnetic substances in the filter cake,“explains Marcus Ludwig from the field sales force of Lehmann-UMT. „The magnetic separator uses a counterrotating pressure roller that ensures the filter cake is dry and that the oil remains in the process.“
After the magnetic separator, the fluid enters an intermediate tank two cubic meters in size, via a baffle plate. Plates fitted at an angle have the function of calming the fluid and preventing the formation of foam, so that the particles are precipitated on the bottom of the tank. The bottom is scraped with a chain conveyor that drops material into the same drum as the magnetic separator. From the intermediate tank, the fluid is then pumped into several filter domes. „The process as undertaken here works with filter cartridges that are periodically flushed from the inside to the outside with a fluid column by pressure surge. A patented process that – unlike the competition – does not take fluid from the clean tank for backwashing. This can quickly amount to 60 litres of fluid, which are then unavailable for the machine supply,“ says Marcus Ludwig. In the StingR, the cleaned medium then goes into a clean tank of approximately 2 m3 in size, from where a pump supplies the four grinding machines. The recleaned medium is discharged at the end by a belt filter, which operates in cycles according to the level or time.
Individual, flexible, adaptable
The ultra-fine filter system was commissioned at the turn of the year 2019/2020. As the project manager, Marcus Ludwig was also the contact person and interface between the two companies from the very first enquiry. “At Gesau, space was a big challenge, so we had consultations about this three or four times,“ he gives as an example. Today, the system runs largely unattended. A service technician visits the company twice a year to ensure machine availability. In addition to on-site maintenance, the machine is also equipped for remote maintenance, so that a technician can quickly connect to the system and rectify any faults. „We guarantee that the machine will be available almost 100 percent of the time,“ Marcus Ludwig says, summing up this point.
The StingR is designed for a throughput of 500 l/min with an oil viscosity of about 15 cSt. Two different types of filter cartridge are installed. The first filters down to a nominal 15 µm, the second to between 3 and 5 µm. „This means that we now have the grinding of HSS with dressable wheels safely under control,“ emphasises Ulf Köhler. There are hardly any expelling losses and the grinding result is better. „Because we filter in several stages, users can target their specific requirements,“ Marcus Ludwig emphasises, „if the user wants to run about 70% HSS and 30% carbide, that‘s no problem for the StingR.“ Ulf Köhler also confirms this advantage: „First of all, it handles the difficult medium safely, but then above all it also offers high flexibility. In addition, we can now select cooling lubricants that may be a better fit for our processes individually for our three systems.“
Marcus Ludwig brings a final decisive point into play – flexibility: „If a manufacturing process changes such that a second or third machine is required, we can expand the filtration system accordingly.“ In addition, it is possible to combine the StingR with other filtration processes to increase their purity levels. „If a user has a large tank, for example, we can increase the previous filtration
level via a bypass.“ In addition to the multi-stage filter technology of the StingR system and its ability to adapt to the respective process, this gives the user additional degrees of freedom to react to
process changes or new requirements. For Gesau-Werkzeuge, this may become interesting in the future in terms of throughput: „We want to further expand the repair of gear-cutting tools in the future,“ says Ulf Köhler. This would admittedly be a modification, but not a metamorphosis.
The medium is collected in 200-litre drums, from which the surface layer can be extracted with a disc pump. The oil recovered in this way enters the intermediate tank, where it is completely cleaned and returned to the circuit (image: Lehmann-UMT)
The recleaned medium is discharged with a belt filter (image: Lehmann-UMT)
The StingR technology
The StingR is an ingenious filter system for maintaining technological equlibriums. The patented process can be used for oil, emulsions or aqueous solutions in the machining of HSS, carbides and even mixed machining. The filter system can be used for grinding, honing and lapping as well as for eroding. Filter finenesses of up to one micrometre can be achieved. The StingR appeals to users with a long service life for the filter elements, high system availability and low energy costs. The system combines short payback times for the investment with high litre outputs in a small installation space.
Learn more!
Book an appointment nowLearn more!